Why Ignoring Minor Maintenance Issues Can Cripple Your Business
For every business owner, it is very important to have smooth operations. Regular maintenance is very important to prevent sudden mishaps. Maintenance tasks keep getting put off time and again in the midst of all the tasks that you need to perform to keep your business afloat and thriving. There could be deadlines to meet, staff demands and customer requirements. However, putting off your maintenance work is never a good idea. Your faucet might be leaky in places and lights might be flickering. These might seem like small things in the larger picture. But ignoring these supposedly insignificant issues can have a cascading effect, leading to major problems and eventually a complete shutdown of your operations.
The reasons for which you should let a professional look into your maintenance needs are discussed below.
1. Small Issues Become Big Problems
A dripping faucet might seem irritating and so you might leave it unaddressed. But it can lead to water damage, mold growth, and even structural problems. A flickering lightbulb might just be annoying,but a faulty wire could spark a fire. These seemingly minor problems can evolve into major expenses and safety hazards.
2. Downtime Disrupts Operations
When equipment breaks down due to a lack of maintenance, your entire operation can stop. Production lines stall, deliveries are delayed, and customer service suffers. This break in operations costs you money in lost productivity and can damage your reputation.
3. Safety Risks
Neglecting safety-related maintenance can have bad consequences. Worn-out fire alarms, malfunctioning electrical systems, or faulty machinery. These situations put your employees and customers at risk of serious injury.
4. Increased Repair Costs
Detecting a problem early is always cheaper than fixing a major breakdown. Constant maintenance at regular intervals helps identify and address issues before they become critical, saving you money. There is a lot of difference between replacing a worn-out bearing and having to replace the entire machine.
5. Higher Energy Bills
Improperly maintained equipment often operates less efficiently, leading to increased energy consumption. Regular maintenance can help optimize energy use, saving you money on your utility bills.
6. Decreased Employee Morale
Working in an environment with constant breakdowns and safety concerns can be demoralizing for your employees. Investing in preventative maintenance demonstrates your commitment to a safe and productive workplace.
Making Preventative Maintenance a Priority
So how can you avoid the domino effect and keep your business running smoothly? The answer lies in preventative maintenance and hiring a professional company. They help you in the following ways-
- Develop a Maintenance Plan- They identify all the equipment, systems, and facilities in your business that require regular maintenance. They also create a schedule for inspections, cleanings, and tune-ups.
- Trained Staff- Companies have staff who are well experienced and are educated. They can identify potential problems and report them immediately.
- Schedule Regular Inspections- Qualified technicians schedule regular inspections. Don't wait for something to break before you call a professional.
- Quality Maintenance Tools- Having the right tools on hand can help professionals address minor maintenance tasks before they become major problems.
Preventative maintenance might seem like an extra cost, but it's an investment in the future of your business. By taking the time to address minor issues proactively, you can save yourself a lot of money, time, and headaches down the road. Don't let a neglected maintenance issue become the domino that topples your entire operation.
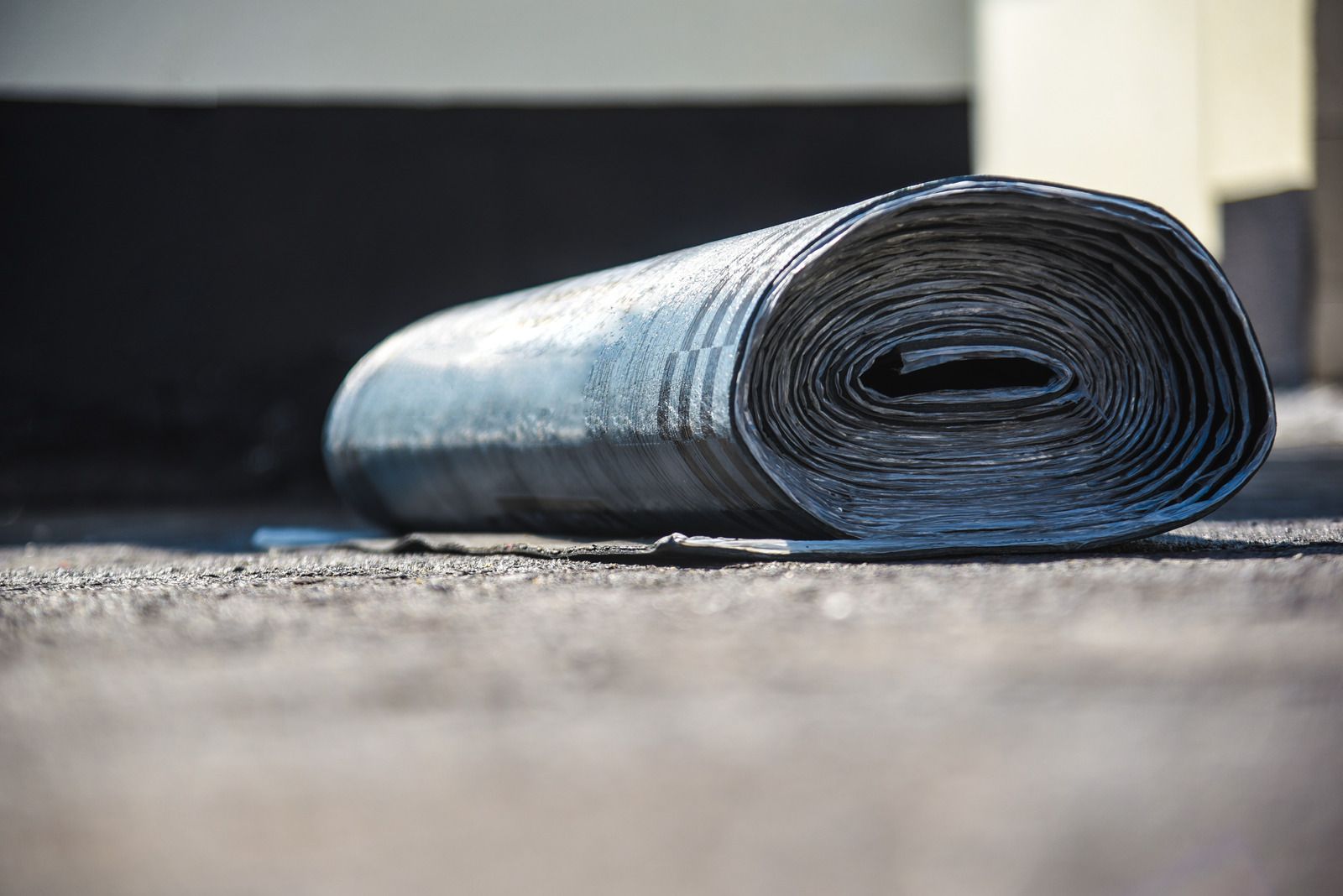